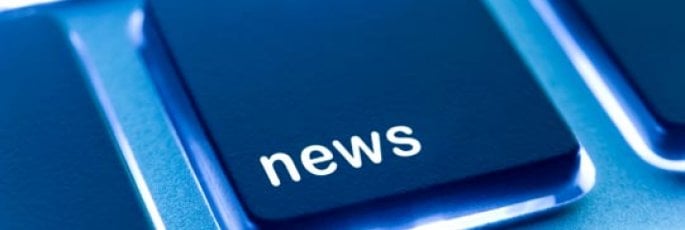
We are Proud to be working with CIMComp -The EPSRC
M Wright & Sons Ltd Research & Development Team within Carbon Fibre Woven structures are proud to be working and supporting the development of Composite manufacture and research within CIMComp
COMPOSITES MANUFACTURING RESEARCH
The development of next-generation composite manufacturing processes to reduce cost, increase performance and improve sustainability.
The EPSRC Future Composites Manufacturing Research Hub was launched in January 2017 and is a £10.3m investment to expand the national research effort towards delivering a step change in the production of polymer matrix composites, whilst training the next generation of composite engineers. The Hub is led by the University of Nottingham and the University of Bristol and initially includes 4 other Spokes; Imperial College London, Cranfield University, the University of Manchester and the University of Southampton. Supported by 4 HVM Catapult Centres and 18 leading companies from the composites sector, collectively offering a further £13m in support, the total portfolio is over £23m. This forms a key element in the UK’s composites manufacturing R&D strategy. The Hub builds on the solid foundations of CIMComp, the previously funded EPSRC Centre for Innovative Manufacturing in Composites, which was set up in June 2011 and ran for 5 years. The Hub aims to become the national centre of excellence in fundamental research for composites manufacturing.
The Future Composites Manufacturing Hub is one of 6 hubs funded by the EPSRC to draw together expertise from 17 universities and 200 industrial partners to strengthen the UK’s manufacturing capabilities and take greater advantage of UK innovation. The mission is to increase collaboration between universities and industry, enabling more products to progress from research labs to market – boosting the UK economy.
New manufacturing techniques for optimised fibre architectures
Aims
- Establish a computational framework for textile preform optimisation not limited by existing manufacturing processes
- Via a series of case studies, identify classes of materials with improved properties over existing forms
- Develop new or modified textile preforming technologies to realise these material forms
- Validate predicted properties and demonstrate performance benefits to materials suppliers and end-users
Methodology
- Develop Texgen to automatically generate non-standard textile formats
- Couple Texgen to a multi-objective genetic algorithm to optimise processing and mechanical properties
- Produce demonstrator samples using a combination of 3D weaving and robotic fibre placement
- Develop laboratory prototypes for new production technologies to manufacture optimised fibre architectures
Pathways to Impact
- Transfer design optimisation methodology to software partner
- Share knowledge with fabric suppliers and end users to embed the approach within industrial practice